
Behind the scenes of the new Topper dinghy design
In 2021, Topper International faced a challenge when the deck mould used in the manufacture of its flagship Topper dinghy was found to have cracked, bringing production to a halt. Until the point the Topper deck mould cracked, production had been continuous for nearly 40 years. Topper dinghies numbered almost 50,000 and were raced across five continents, with all boats having been manufactured from what were, certainly for a time, the world’s largest injection moulds.
These tools and the process had revolutionised boat production when it was first set up in 1976 – their original lifespan was predicted to be around 10,000 Toppers.
Topper dinghy – the history
Taking just eight minutes to produce a hull and a deck using twinned kirksite moulds, the 3.4 metre long, 1600 tonne machines produced matched parts, accurate to within 0.020in, using a series of hot and cold ‘runners’ to aid material flow and with injection speed carefully monitored to ensure uniformity.
Hull and deck were self-coloured, UV stable and required no finishing or painting, eliminating delays associated with conventional boat manufacture. Using an electrical fusion technique (later patented) to seal the hull and deck together, the full assembly and fit out process took less than three hours. For the first time, boats could be sold from stock – ideal for export.
The process allowed boats to be made from polypropylene, meaning they were lighter and significantly more robust than the original glass fibre model (known as the OD11, which had been developed from an original wooden prototype, in 1969).
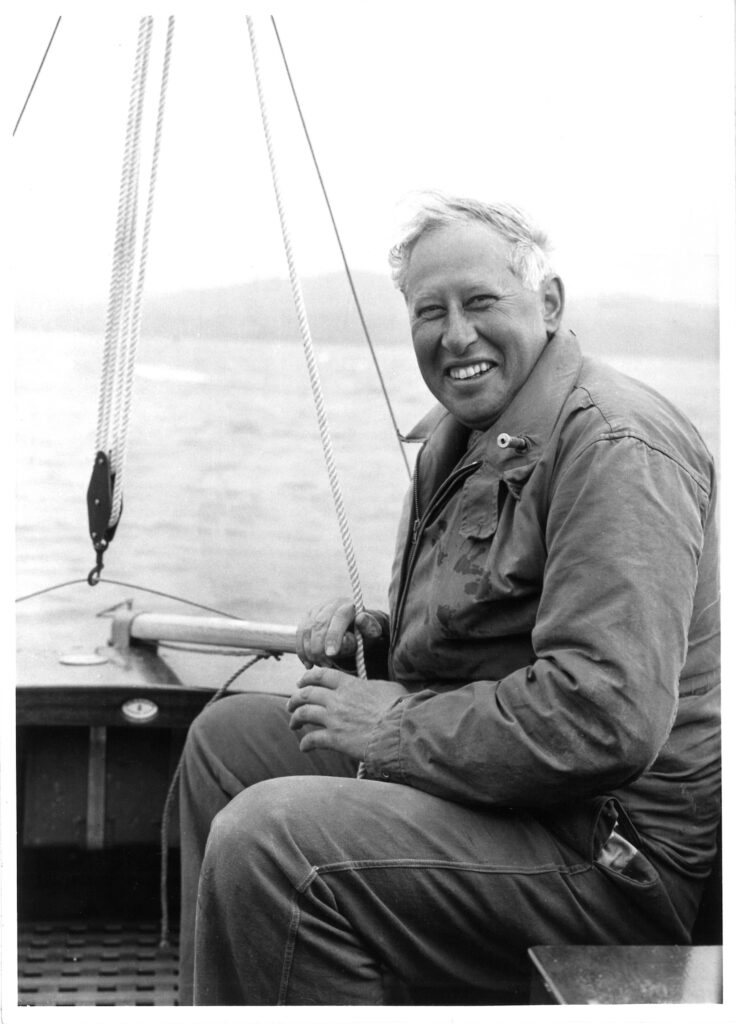
Maurice Robin, a pioneer in new technology for use in the automotive industry, had proposed the concept to Topper designer Ian Proctor (left) at the 1973 London International Boat Show. His company, Rolinx (a subsidiary of ICI), was a leader in the injection moulding industry. Proctor – a keen innovator as well as Yachtsman of the Year and a Royal Designer for Industry – immediately saw the potential. Funding was sought from the National Enterprise Board, ICI and Guinness, with the machine costing £1.5m in today’s terms. Manufacture took place at Dunhill Boats, with the Topper credited at the time as the largest injection moulded product in the world.
Not only did the boat win multiple design awards, including the 1977 Design Council Design Award, but it led to a worldwide proliferation of the class that was unprecedented in the dinghy market.
Production remained at Dunhill Boats until the mid-1980s when it was taken over by Topper International Ltd and manufacture switched to Germany. The class received ‘international’ status from World Sailing in 1994 and is also an RYA Junior Pathway class. It has been the proving ground for many Olympic sailors. In 2012 the Topper was further celebrated when it was displayed in the V&A museum in London and also in the Science Museum, in a dual celebration of British design and innovation.
The new Topper design
Today, with huge investment from Topper International and working in close consultation with Ian Proctor Designs (the licensor) and Roger Proctor, the popular recreational and racing class has been granted a bright future.
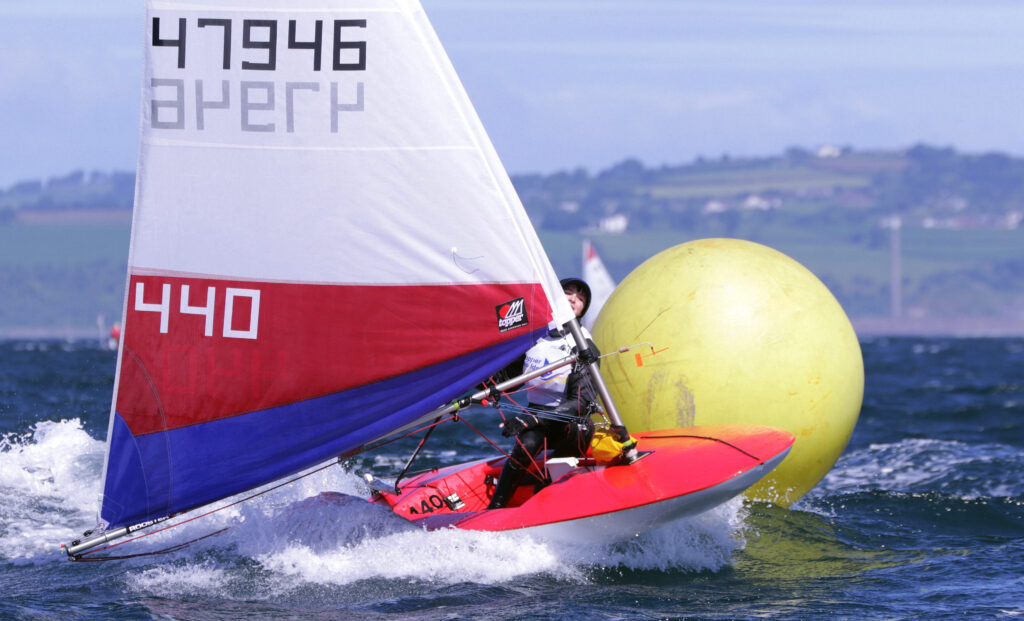
With the cost of repair to the original moulds estimated at £1.5-2m, and with pressure to increase production volume from the moulding factory, Topper International looked to alternative manufacturers; however, the size of the mould limited options.
Further alternatives included replacing part of the cracked mould, manufacturing in glass fibre or three-part moulding in polypropylene, but these were dismissed for practical and sustainability reasons. Instead, a more modern method of rota moulded polyethylene was chosen, drawing on Topper International’s 25 years of expertise in manufacturing their Topaz range of dinghies and catamarans and bringing the boat in line with most contemporary dinghy designs.
Manufactured in one mould, with hull and deck produced as one sealed unit, the rota moulded Topper is made using a three-layer TRILAM sandwich in a process unique to Topper International. The multiaxial moulding process is computer controlled to ensure consistent distribution of sugarfine powder to form the layers; foaming agent is added to the central layer which creates a dense ‘honeycomb’ core to ensure rigidity of the hull. A specialist cooling jig regulates shrinkage and ensures uniformity of weight.
Ensuring the original design and performance remained unaltered to preserve the boat’s one-design status was crucial; Topper says that extensive on-water testing, at both inland and at coastal venues, proves this has been achieved. As part of this, the Topper’s original soft leach sail and anodised two-part rig have been retained. Brass fittings incorporated into the hull moulding have increased strength, while minor adjustments to the selfbailer positioning and cockpit ergonomics have increased sailor comfort; hatches have been included to aid the production process and can be converted for storage of small items.
On-demand production and fit out of the new boat now takes place wholly within the UK, streamlining logistics. Although the overall production process is longer, increased efficiencies mean that the builder says the cost of the new process has not been passed onto the consumer.
Futureproofing a classic
The new rota moulded Topper was launched at the RYA Dinghy and Watersports Show in March 2023 with a distinctive grey colourway giving a futureproof aesthetic.
The update has been approved by World Sailing and class associations worldwide, and demand for the new boat has come from clubs, export dealers and individuals.
In July 2023, the Topper World Championships was held at the Royal Cork Yacht Club, Ireland. Of the 261 boats competing approximately 80 were the new Topper rota moulded model. Roger Proctor says his father would have approved of the move to a modern production method, and he applauds “the investment made by Topper International to secure the future of the much-loved class for both racing and recreational sailors for generations to come.”
Read more articles in Marine Industry News magazine.
The post Behind the scenes of the new Topper dinghy design appeared first on Marine Industry News.